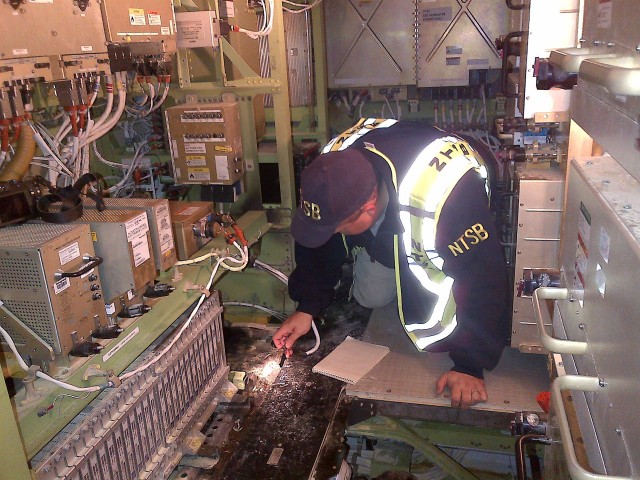
Bad battery design and bad engineering practices were to blame for the fire aboard a Japan Airlines Boeing 787 in Boston in 2013, according to a final report (PDF) on the incident issued by the National Transportation Safety Board (NTSB) yesterday. The NTSB found fault not only with the manufacturer of the battery, but with Boeing and the Federal Aviation Administration (FAA).
In a prepared statement, NTSB Acting Chairman Christopher A. Hart said, “The investigation identified deficiencies in the design and certification processes that should have prevented an outcome like this. Fortunately, this incident occurred while the airplane was on the ground and with firefighters immediately available."
There are two battery systems aboard the 787: the “main battery” in the front of the aircraft, which powers the 787’s ground maintenance systems and provides backup power to the aircraft’s control systems, and another set in the aft end of the aircraft used to start up the 787’s auxiliary power unit (APU), a small turbine engine in the aircraft’s tail which provides electrical power. Both systems used the same types of lithium-ion batteries manufactured by the Japanese firm GS Yuasa. And while the APU batteries were at fault in the Boston fire, a main battery caught fire two weeks later on an All Nippon Airways flight in Japan.
Thermal runaway
Both fires were the result of “thermal runaway”—the batteries became overheated to the point where a chemical reaction was triggered that released even more heat, causing a cascading effect that caused the batteries to explode or catch fire. Because of the fire hazard associated with lithium-ion batteries, there have been concerns about them being carried on airplanes—let alone being used as part of their electrical system—since 2004, when a battery caused a fire on a FedEx cargo plane.
In its report on the Boston fire, the NTSB cited thermal runaway as the cause, finding “[s]afety issues related to cell internal short circuiting and the potential for thermal runaway of one or more battery cells, fire, explosion, and flammable electrolyte release; cell manufacturing defects and oversight of cell manufacturing processes.” There were also concerns over the engineering that went into “thermal management” of the “large format” lithium-ion batteries aboard the aircraft.
Thermal runaway can be caused in a number of ways—most of them related to a short circuit within the battery itself. Manufacturing errors, including deformations caused in assembly and poor quality control, can create conditions which lead to internal short circuits in lithium-ion batteries, as can the swelling and shrinking of battery cells as they are charged and discharged. An analysis of the batteries involved in the fire found evidence of lithium metal deposits called lithium dendrites, which can grow over time from the battery’s anode and cause an internal short circuit, as well as reacting chemically with the battery cell’s electrolyte in a way that creates more heat. The dendrites were found to occur in wrinkles found in some of the electrolyte material formed while it was being wound—a serious quality control issue.
NTSB recruited Underwriters’ Laboratories (UL) to conduct a “short circuit abuse” test using cells of a battery provided by Boeing. The testing “showed that conduction of the heat generated by an internal short circuit in one winding of a parallel arrangement to adjacent windings could cause thermal damage in those windings and lead to thermal runaway of the entire cell,” the NTSB report noted.
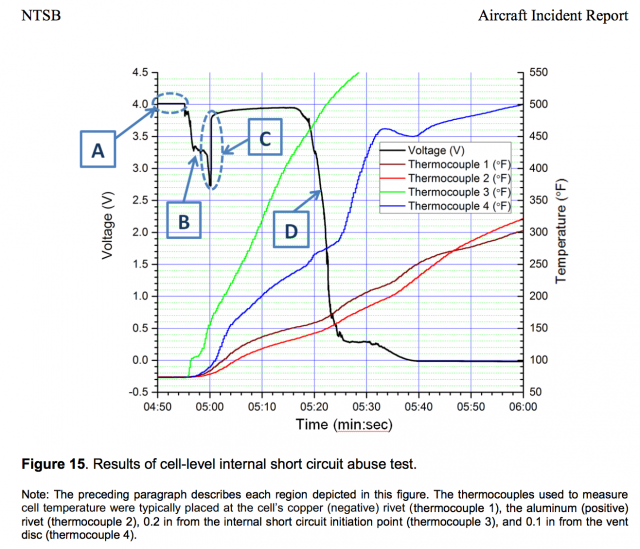
But the NTSB also found shortcomings in the FAA’s guidance to manufacturers on factors to consider in safety assessments of equipment, as well as the agency’s guidance to its own certification engineers “to use during the type certification process to ensure compliance with applicable requirements.” And the NTSB cited problems with the 787’s enhanced flight data recorder, which resulted in “stale flight data and poor-quality audio recording.”
Failure to audit
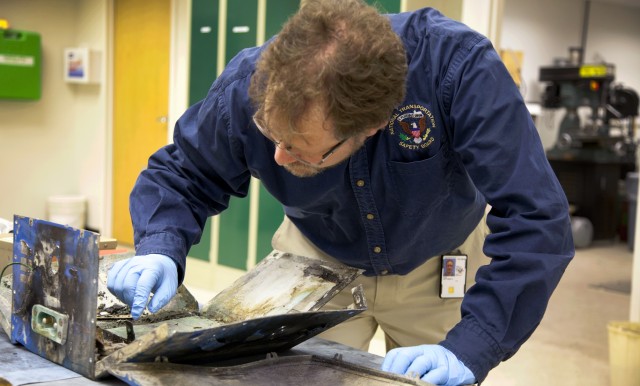
Part of what led to Boeing and the FAA failing to catch manufacturing issues at GS Yuasa was the way the 787 was built. The electrical systems for the 787 were outsourced to Thales, which in turn was responsible for managing each of its own suppliers and ensuring they met Boeing standards. But Thales apparently made some changes to things in its systems without a Boeing sign-off, and GS Yuasa made some changes of its own that deviated from Boeing and Thales' instructions.
When the FAA and Boeing finally did perform audits on GS Yuasa, they found a raft of problems. The FAA found GS Yuasa’s operation wasn’t following instructions on battery component assembly and installation, wasn’t properly labeling parts, and that there was “no traceability [of component and assembly part markings] to assembly drawing and instructions,” according to the NTSB report.
Boeing found 17 specific issues. “Most of the noncompliance items at GS Yuasa involved adherence to written procedures and communication,” the NTSB report stated, and the “non-compliance items at Thales involved adherence to contractual requirements for Boeing’s approval on drawing or procedural changes.”
These issues will no doubt cause a chorus of “I told you so” from many—including some Boeing workers—who have opposed Boeing’s global approach to assembling the 787. By spreading the work into a modular process across multiple subcontractors and leaving only the final assembly of the aircraft to its own workforce, Boeing hoped to save significantly on manufacturing costs. But the battery problems as well as more recent issues with cracks in the wings of aircraft still in the assembly process have caused long delays in the 787’s full rollout, leaving customer airlines waiting and potentially costing Boeing billions of dollars in future sales.
Listing image by Spaceaero2
reader comments
76